Integrating lean coaching principles into Medtronic with lean six sigma
As the world’s leading medical device company known for its breakthrough technologies and solutions, Medtronic wanted to bring together the principles of coaching and integrate them with Lean Six Sigma. They asked Performance Consultants to design and deliver a leading edge global learning programme that could be deployed at scale, within an 8-week deadline.
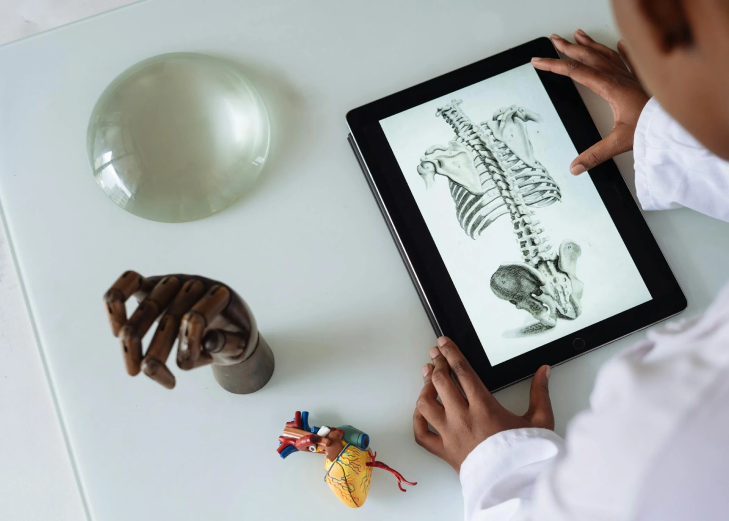
This programme ensures empathy, heart and purpose is right at the centre of Lean, and gives practitioners a turbo boost to improve performance.
By equipping them with coaching skills that perfectly complement what they are already doing, both Lean practitioners and their teams feel more empowered, more engaged and able to do more with less.”
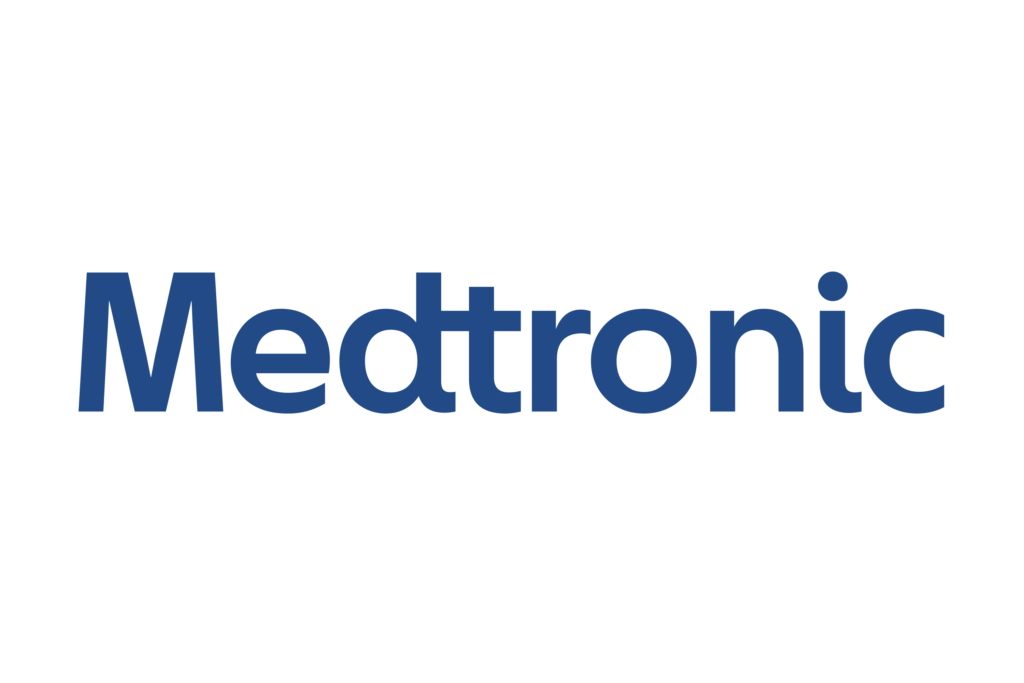
The Client
Medtronic, Inc. is the world’s premier medical technologies, services and solutions company operating in approximately 160 countries and employs just under 100,000 people. It contributes to human welfare by applying biomedical engineering in the research, design, manufacture and sale of instruments or appliances that alleviate pain, restore health and extend life.
As part of the Medtronic Mission, the company recognizes the personal worth of all employees by providing an employment framework that allows personal satisfaction in work accomplished, security, advancement opportunity, and means to share in the company’s success.
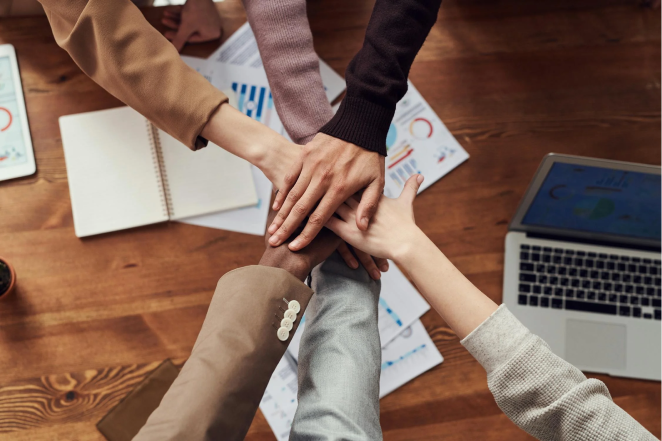
The Challenge
Medtronic wanted to create an environment where innovation, ownership and learning thrived in Lean Six Sigma implementation. Running the most optimized and efficient processes possible in its global medical devices manufacturing plants and core financial processes was imperative.
They were looking to:
Integrate Lean coaching principles with Lean Six Sigma implementation in their manufacturing plants
Create a blended Virtual programme to support new Performance Conversations that could be deployed at scale across the organization.
Rapidly support their 500 leaders in the Diabetes division having a new type of year end Performance review that focused on the ‘how’ as well as the ‘what.’
We had 8 weeks to design and deliver coaching training that would give leaders what they needed.
Employees who know they’re supported are going to be more committed to the organization, and we will see that return reflected in employee engagement”
Our Approach
Working closely with Medtronic’s Diabetes division, Enterprise stakeholders and their Coaching Centre of Excellence, Performance Consultants co-created a modern and leading edge global learning programme that could be deployed at scale.
The new year-end performance reviews eliminated the traditional rating-based performance management system. Medtronic wanted to go back to basics – providing employees with feedback on their performance and supporting them in achieving their goals. As a result they moved away from competitive assessment and towards providing real time performance feedback, coaching and development sessions for employees.
Performance Consultants designed and delivered a practical 5 step training programme based on coaching mindset and behaviours to leaders created out of the principles of Awareness & Responsibility, and the GROW model to enable individuals and teams to find and implement their own solutions.
We co-designed and delivered 90-minute live experiential interactive Virtual sessions for 100 leaders at a time, supported by podcasts and workbooks. The content was later wrapped up as a training program and deployed as a learning campaign to all 10,000 people leaders within Medtronic.
The program focused on the practical application of coaching to Lean management. For example, it included a game which replicates a typical production line where a specific output has been requested and where penalties will be incurred for missed quality targets. Within it, continuous improvement of performance is a requirement just as it would be in the workplace.
The aim was to provide an opportunity to practise coaching skills and behaviours immediately, in an environment that reflects normal working conditions rather than a traditional training room, as well as demonstrate the impact on performance and learning for participants.
The enterprise loved it as they realised that a coaching style of leadership is the perfect complement to Lean as the core principle of Lean is continuous improvement. This is in perfect alignment with one of coaching’s cornerstones – learning.
In Lean, the process for achieving this continuous improvement is through:
- Gaining awareness of what is/isn’t working
- Using the individuals and teams within the direct production area as experts
- Identifying ways to build further on strengths and improve areas of weakness
This mirrors Performance Consultants’ approach to coaching within the workplace.
The programme was rolled out to all 10,000 leaders globally.
Together, Lean and coaching create a virtuous circle of unparalleled performance improvement. Organizations and teams which use Lean principles can create the ideal conditions for a true learning environment and maximum performance if they also bring in a coaching style of leadership.”
The Results
Participants reported noticing where coaching skills could be applied in their day-to-day work and said they felt more equipped to facilitate everyday interactions, built new awareness in their teams and increased their sense of responsibility to take personal action.
Despite the initial concerns of eliminating the rating-based system, employee engagement surveys and focus groups have shown that the whole organization is more satisfied with the new process.
Managers now use a coaching style of leadership to support employees to achieve their objectives and pursue individual career development. Performance reviews are no longer about managers giving a rating; employees are coached on how to improve future behaviours. Medtronic calls this new process “Performance Acceleration” as it focused on an individual’s performance in relation to specific business objectives. Employees are encouraged and coached on creating objectives that are aligned with critical business activities.
Medtronic has also added a recognition program called “eMpower” to drive 3 key elements of employee engagement: fostering participation, recognizing performance, and maximizing employee potential.
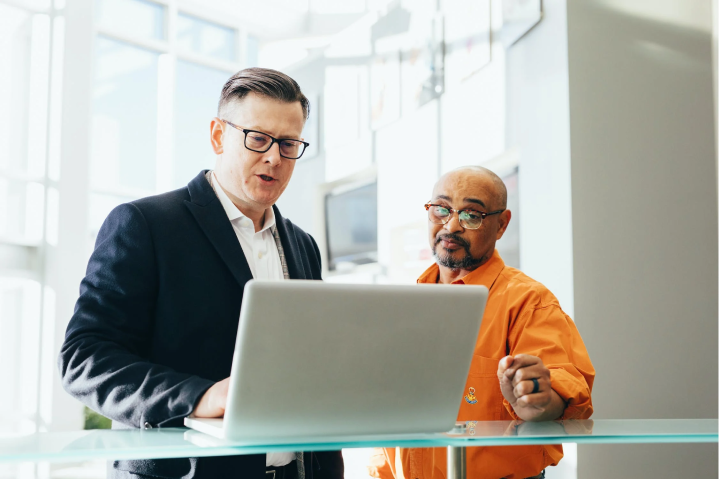
Discover coaching training
If your organization is inspired by Medronics story, explore our industry leading coaching training program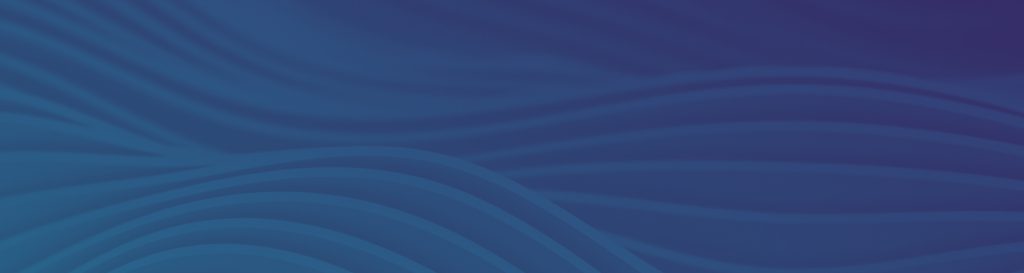